Industry Trends7 min
Can Structural Solutions Products Be Used in Commercial Builds?
Drive through your town's central business district and instead of soaring commercial buildings of steel and glass, you'll likely see coffee shops, fast-casual restaurants, small retail stores, schools and possibly a mixed-use multi-story complex. Many commercial builders opt for premium engineered wood products, such as those in the LP® Structural Solutions portfolio, as their primary commercial building materials, chosen for strength, versatility, consistency, labor savings and more.
Just as not all commercial buildings are steel and glass, not all commercial building materials or sustainable building materials for commercial buildings are strictly designated for either commercial or residential use. Let's take a look at the benefits of using engineered wood in commercial building applications.
Diversity of Engineered Wood as Commercial Building Materials
Today, the engineered wood category includes oriented strand board (OSB) in addition to the traditional engineered wood products: laminated strand lumber (LSL), I-joists and laminated veneer lumber (LVL). These building materials allow for faster, more economical construction.
As building codes allow the use of wood in larger five- and six-story structures, commercial builders are constructing a variety of wood office buildings and retail standalone stores, so engineered wood products continue to find more applications.
LP Building Solutions is among the top commercial building material suppliers. The company started its manufacturing legacy 50 years ago with the original OSB.
Over the last few years, commercial builders have taken note of the innovations of the LP Structural Solutions portfolio. Structures of all sizes and configurations need strong code-compliant materials that guard against water intrusion and help protect against fire.
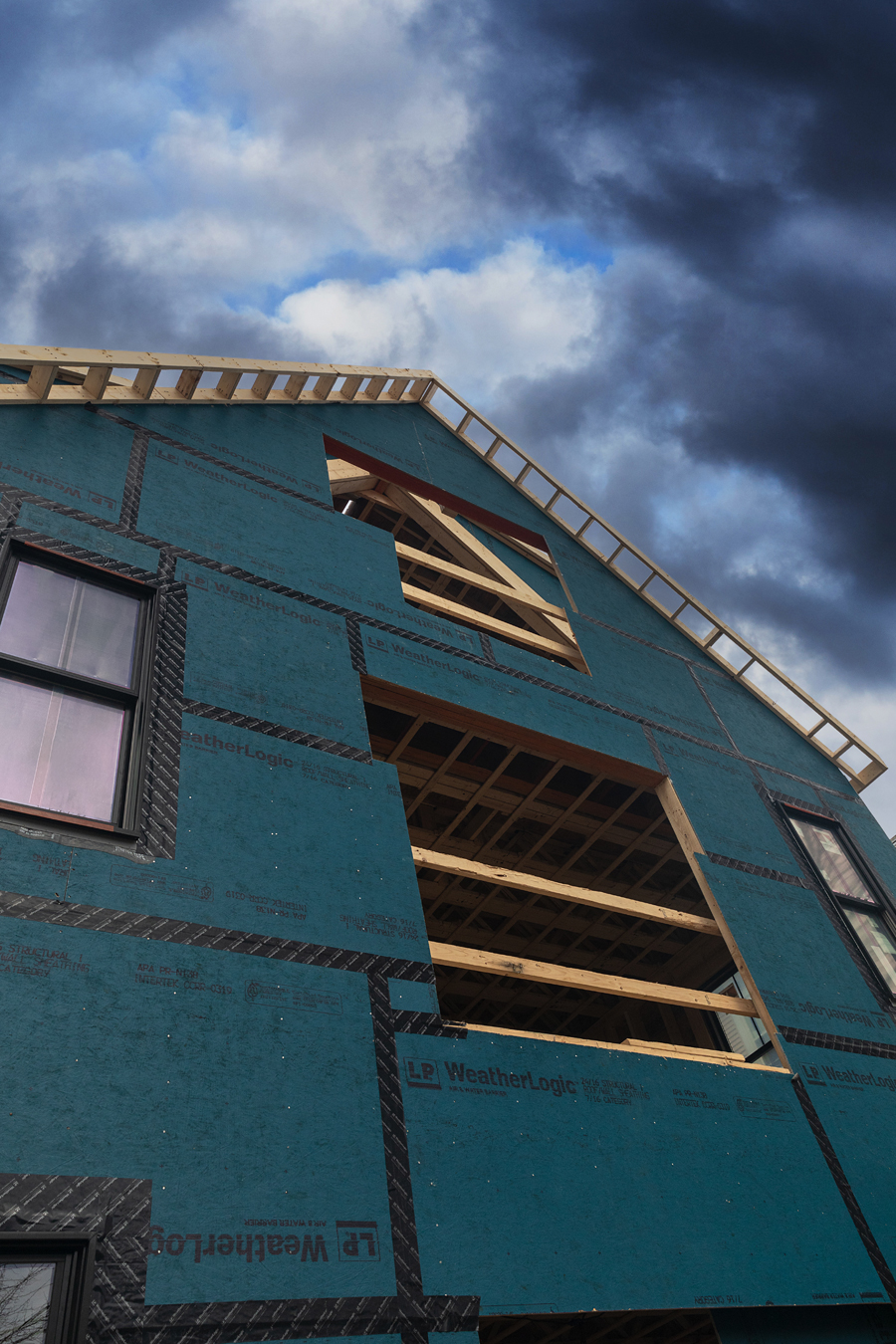
Benefits of Engineered Wood Products
Engineered wood plays a dominant role in numerous construction applications, beginning with concrete forming and structural framing. Wood components can speed up construction due to ease of cutting and fastening.
Engineered wood materials offer many advantages over traditional wood products, including:
Engineered wood randomizes the strength-weakening defects in solid wood (knots and slope of grain, for example) to help maximize strength and stiffness.
Low manufactured moisture content helps provide dimensional stability to reduce shrinkage, warping and twisting as traditional wood products dry after installation.
Engineered wood comes from renewable sources, making it more sustainable. There may be more credits for wood-based materials when assessing compliance with green building codes.
CASE STUDIES: HOW COMMERCIAL BUILDING MATERIALS ARE USED
Choosing Strength and Versatility in Standalone Commercial Building
Kyle Stumpenhorst, contractor and founder of RR Buildings, turned to the Structural Solutions portfolio when he constructed a standalone commercial building.
“Anytime I've installed LP Legacy sub-flooring, I've always thought I was standing on concrete once it was installed because it is so solid,” he adds.
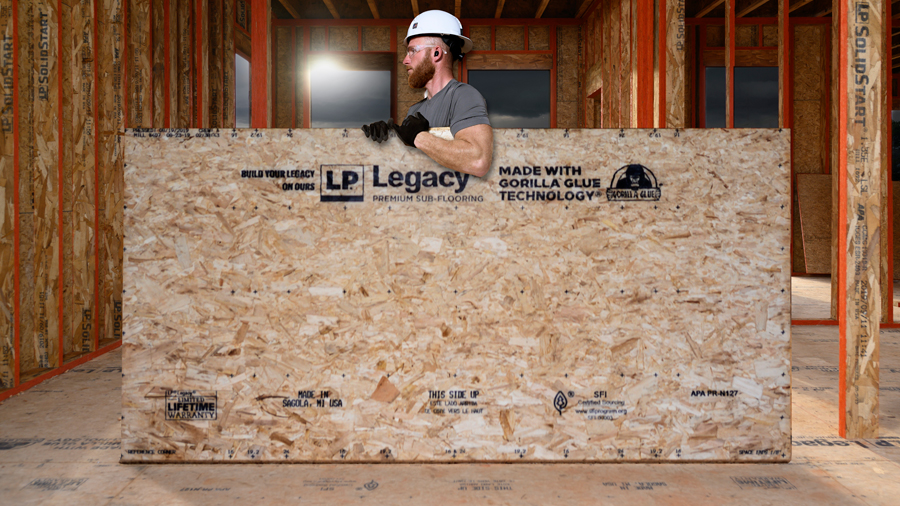
Rated for roofs and walls and designated Structural I, LP WeatherLogic® Air & Water Barrier is built for enhanced structural capacity and protection from water intrusion. The LP WeatherLogic system helps create a tight building envelope that helps offer energy efficiency to the owners. It installs like regular sheathing so Stumpenhorst benefited from an integrated water barrier and strong structural element for the build. “You don't have to come behind it and add a water-resistive barrier (WRB). You've got a system that combines the structural panel with a built-in WRB,” he says.
Concrete vs. Engineering Wood: Limiting In-Field Construction Costs
When building affordable living spaces inside urban areas, it's important to keep construction costs manageable. To do so, Avalon Bay construction firm and national architectural firm KTGY selected LP® FlameBlock® Fire-Rated OSB Sheathing to meet Type III wood frame construction code requirements.
“LP FlameBlock Fire-Rated Sheathing combines the flame spread resistance we need with the structural performance of OSB,” said Rick Morris, the senior vice president for Avalon Bay.
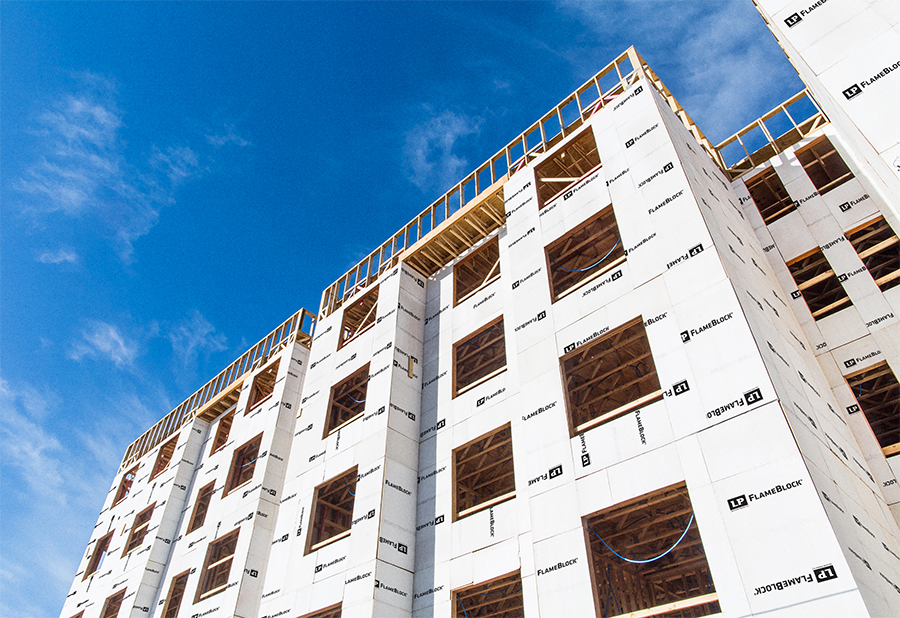
Rohit Anand, principal architect for KTGY, echoed Morris's sentiment: "In Type III construction, you need to meet code, including fire and lateral bracing requirements. LP FlameBlock OSB is a composite product that really takes care of both needs in one application step."
LP FlameBlock Fire-Rated Sheathing features LP's proprietary non-combustible, fiberglass-reinforced Pyrotite® coating and is evaluated to meet code requirements for fire-resistant construction. It also does not require reductions in strength, offering the versatility to be used in all types of construction as a listed component in fire-resistance-rated wall assemblies.
"We have one of the largest development platforms and continue to do more high-density wood construction in infill locations," Morris said. "We're building five- and six-story buildings. LP FlameBlock Fire-Rated sheathing helps us go high and provide more density. We don't have to go to concrete or some of the other materials that are more costly and challenging to work with."
Because LP FlameBlock panels are installed with the same tools and fasteners used for installation of other structural sheathing, Morris said his carpenters who are familiar with wood construction have not experienced any issues when installing the product.
"I think that with Type III construction becoming more and more prevalent, a product like LP FlameBlock Fire-Rated Sheathing will be used a lot more. It makes construction easier," Anand said. Because LP FlameBlock sheathing is able to offer a fire-resistance rating as well as structural integrity in a single panel, both firms plan to use the product on future commercial projects.
Need to curb construction costs? Dig into advice from construction pros like you on ways to lower costs and handle constructor labor shortages on the jobsite.
Continue Reading
Resiliency Solutions
5 minIntroducing LP® SmartSide® ExpertFinish® Naturals Collection™: Nature-Inspired Beauty Meets Engineered Performance
We're excited to introduce the LP® SmartSide® ExpertFinish® Naturals Collection™, a bold new addition to our trusted line of engineered wood siding and trim that delivers the warmth and beauty of nature with the advanced protection and performance builders and homeowners expect.
Labor Solutions
5 minChoosing the Right LP® Structural Solutions Product for Your Build
When it comes to building strong, reliable, and high-performing structures, the materials you choose matter. At LP Building Solutions, we understand that every project, whether it's a single-family home or a multifamily development, requires structural components that meet your needs for strength, durability, and efficiency.
Sustainability Solutions
5 minBuilding a More Sustainable Future with LP Building Solutions
In today's world, sustainability is no longer just a buzzword, it's a blueprint for responsible living and smarter building. As the construction industry seeks ways to reduce its environmental footprint, LP Building Solutions is focused on providing innovative building materials for eco-conscious builders to help reshape what it means to build sustainably
News & Stories3 min
History of Partnership with Gary Sinise Foundation
The LP Foundation is a proud partner of the Gary Sinise Foundation, which supports wounded veterans in several ways. You can learn more about the LP Foundation here.