Business Advice5 min
When to Use Insulated OSB Sheathing
There are many insulation options available, including traditional batting, cellulose, fiberglass and mineral wool. While building codes typically dictate the specific R-values needed, many builders are using materials that enhance homeowner comfort and green building programs. We caught up with Neil Freidberg to learn more about the factors influencing R-value.
Freidberg is a Building Science Manager at LP Building Solutions, and for the past 10 years he has been deeply involved in examining R-values and building insulation methods.
What is R-value?
R-value is the thermal resistance value based on a material's properties and thickness. Essentially, it's a measure of thermal resistance and how well a particular material keeps heat from moving into or out of a structure.
While we're used to thinking about traditional batting for R-values, all building materials—including wall sheathing, studs and drywall—have an R-value, but they contribute minimally to the total R-value for a home.
What Factors are Involved in Choosing R-value?
"One of the factors in choosing R-value is how it captures and traps air," says Freidberg. "In a closed foam material like XPS, it traps a combination of blowing agents and air in cells to increase the resistance to heat transfer."
The factors involved in choosing R-value depend on where you live. Most of the climate zones within the U.S. specify the R-value for exterior walls to be between R-13 to R-30. This is where continuous insulation comes into play in many climate zones.
What is continuous insulation? Continuous insulation encircles the exterior of a framed structure. Because this insulation is not sitting in between the studs, but rather outside of the studs, it provides a continuous, uninterrupted layer of insulation around a home.
What is the Benefit of Insulated Sheathing Board over Traditional Methods?
The key to better insulation performance is continuous insulation, which can be achieved with insulated sheathing panels. While continuous insulation is required by code in some areas, one benefit is it decreases thermal bridging.
Thermal bridging happens when heat finds a path in or out of a building due to an interruption in, or insufficient amount of, insulation. Typically, this heat transfer occurs through the studs or framing members.
Friedberg explains it further: "Wall assemblies have cavities and studs. Cavities can be insulated at R-13 to R-15 for a 2x4 wall. But that doesn't mean the entire house is insulated to R-13 to R-15. Even wood has a minimum R-value, but it's roughly R-3.5. Since studs make up 25 percent of your house, that means 25 percent is insulated at R-3,5 rather than R-13 to R-15, reducing the overall performance to R-9 and R-11.
"By adding insulated sheathing--or continuous insulation--you are decreasing thermal bridging and increasing the R-value so you can have an R-14 to R-16 exterior wall," he says. "In climate zones 4 to 8, builders are required to put in continuous insulation, which is R-5 or higher. In the 2x4 wall assemblies, you can use an R-15 batt in combination with the R-5 continuous insulation--making it a nominal R-20."
Benefits of Continuous Insulation
"When using continuous insulation, the biggest benefit is a more comfortable house for the homeowner. Insulated panels reduce heat gain or loss through the studs," says Freidberg. "It affects the cost to condition the interior rooms and improves the comfort for the occupants. It helps the interior rooms stay warmer longer in the wintertime and stay cooler longer in the summer."
To help you enhance the comfort level of your homebuyers' homes, this summer LP will be introducing LP NovaCore™ Thermal Insulated Sheathing, an innovative, dual-layered structural OSB and XPS foam designed to protect structures against heat loss and gain. The insulated wall panels can be handled, cut and drilled like OSB, making them easy to install while delivering an R-value of 5 per inch of thickness.
Freidberg is noticing more interest around insulated OSB sheathing as green energy programs and net zero builds continue to gain popularity around the U.S.
Learn how LP Building Solutions is part of the ever-expanding future of green homebuilding.
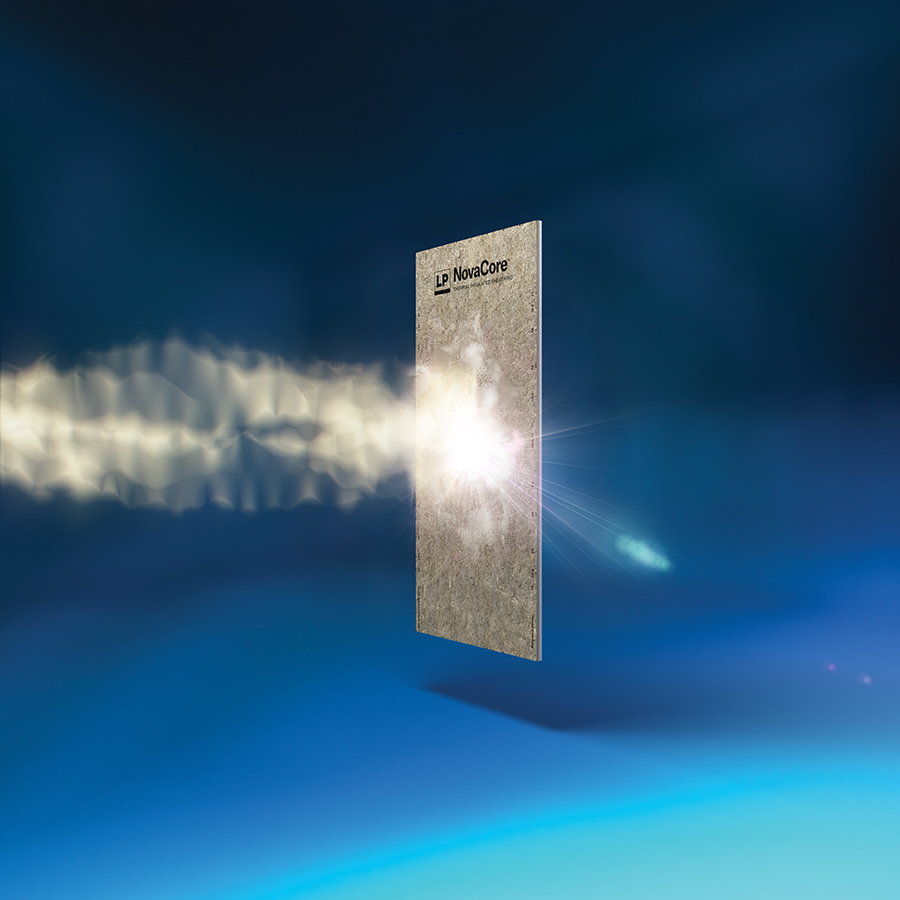
Continue Reading
Resiliency Solutions
5 minIntroducing LP® SmartSide® ExpertFinish® Naturals Collection™: Nature-Inspired Beauty Meets Engineered Performance
We're excited to introduce the LP® SmartSide® ExpertFinish® Naturals Collection™, a bold new addition to our trusted line of engineered wood siding and trim that delivers the warmth and beauty of nature with the advanced protection and performance builders and homeowners expect.
Labor Solutions
5 minChoosing the Right LP® Structural Solutions Product for Your Build
When it comes to building strong, reliable, and high-performing structures, the materials you choose matter. At LP Building Solutions, we understand that every project, whether it's a single-family home or a multifamily development, requires structural components that meet your needs for strength, durability, and efficiency.
Sustainability Solutions
5 minBuilding a More Sustainable Future with LP Building Solutions
In today's world, sustainability is no longer just a buzzword, it's a blueprint for responsible living and smarter building. As the construction industry seeks ways to reduce its environmental footprint, LP Building Solutions is focused on providing innovative building materials for eco-conscious builders to help reshape what it means to build sustainably
News & Stories3 min
History of Partnership with Gary Sinise Foundation
The LP Foundation is a proud partner of the Gary Sinise Foundation, which supports wounded veterans in several ways. You can learn more about the LP Foundation here.