News & Stories6 min
How is Engineered Wood Made?
When it comes to wood products, all builders want to make sure they're using the best options available. That's where engineered wood comes in-but what exactly does it mean for a wood building product to be "engineered"? And why does it matter for a builder looking to create structures that last?
Here, we'll break down LP's manufacturing process for engineered wood, from sheathing to siding and more, to show you why engineered wood serves as one of the most trusted building solutions on the market.
What Is Engineered Wood?
Engineered wood refers to building products that are made by binding wood fiber (in the form of strands or veneers—strands in the case of OSB) with moisture-resistant structural adhesives and orienting the fiber in specific directions to achieve desired strength, stiffness and stability.
This also randomizes the natural characteristics of solid wood such as knots and irregular grain, minimizing the impact on strength. Simply put, with engineered wood builders can get the sustainability of a naturally occurring product-wood-with increased uniformity and performance. Let's examine the details of engineered wood made by LP by tracking the engineered wood manufacturing process.
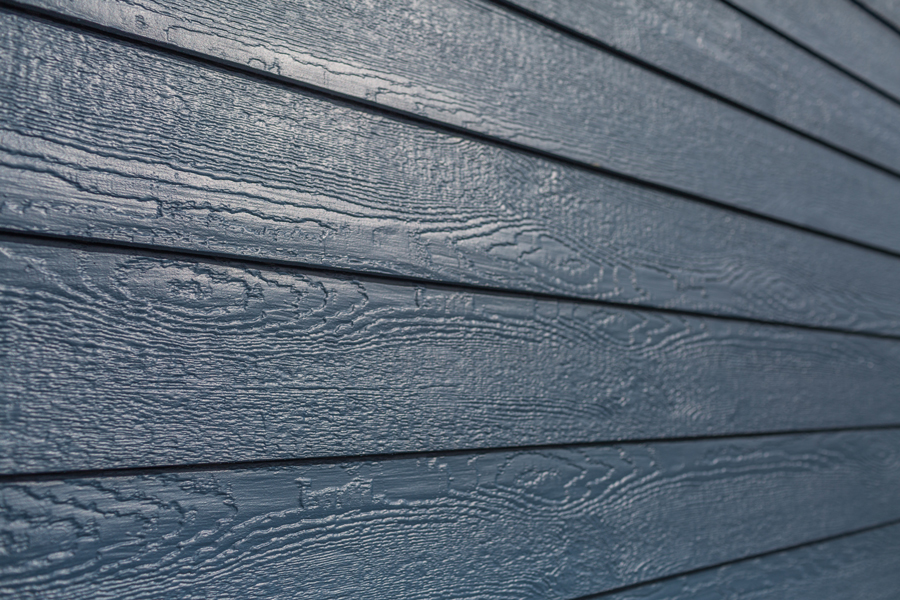
Step 1: Sourcing Wood Strands for OSB Production
LP engineered wood products are sourced from sustainably managed forests, and LP's products are certified by the Sustainable Forestry Initiative® as produced from wood that comes from responsibly managed forests. This helps to ensure resources are available for future generations. In fact, four million trees are replanted annually in the forests that LP manages in Canada. From the beginning, LP uses 99 % of harvested wood fiber during the manufacturing process, either in the products themselves or as a thermal energy source for the manufacturing facilities.
In the case of LP® SmartSide® Trim & Siding, the product is one of the only carbon-negative siding products on the market. This means that it stores more carbon than it releases during production and distribution. Check out LP SmartSide siding's Environmental Product Declaration here.
Read more about our environmental policies here.
Step 2: Preparing the Wood Strands
To start the manufacturing process, conditioning ponds are used to soften and condition logs so that the wood fiber can be brought to a more uniform temperature for stranding and the bark can be more easily removed. The removed bark is then used as a heat source for the manufacturing facilities.
Next, logs are machined into strands that are screened for the proper size. Then, usable strands are dried to a desired, consistent moisture level to facilitate downstream processes. Strands not used for engineered wood products are used for fuel.
This is the beginning of our unique engineered wood manufacturing process.
Step 3: Adding Value for Strength and Moisture Resistance
At this point in the process, our engineered wood products are truly set apart as value-added, advanced proprietary solutions for builders.
For example, when it comes to how engineered wood siding is made, the LP® SmartGuard® Process takes place at this stage. During the manufacturing of LP SmartSide Trim & Siding, strands are coated with waxes and zinc borate that work together to help prevent moisture intrusion and to help resist fungal decay and termite damage. This makes it one of the most durable siding solutions on the market.
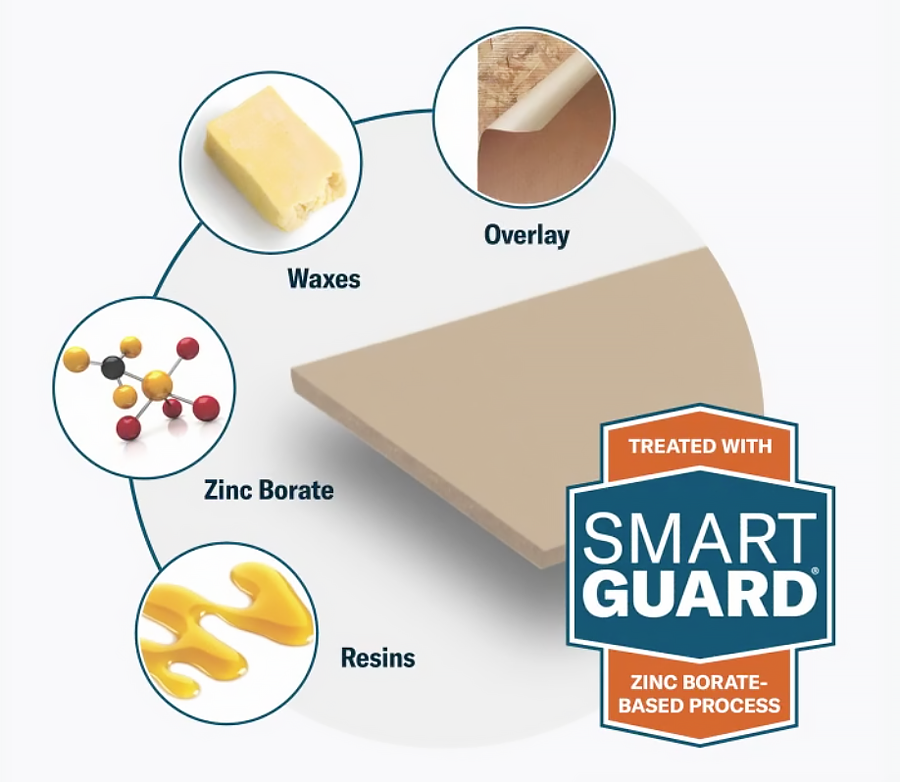
LP Legacy® Premium Sub-Flooring serves as another example of how engineered wood sub-flooring is made. To achieve the engineered properties of LP Legacy sub-flooring, generous amounts of strands are first heavily coated with a highly moisture-resistant resin, which uses Gorilla Glue Technology®.
After all additives have been incorporated, the strands are then oriented and layered intentionally to achieve desired directional (along and across-panel) bending properties and dimensional stability.
Step 4: Pressing and Finishing
Next, the material is consolidated under specified amounts of pressure and heat. In the case of LP Legacy sub-flooring the panels are sanded to a uniform thickness, machined with a self-spacing tongue-and-groove profile, and sprayed with a premium edge sealant. The end result is an engineered structural sub-flooring with superior stiffness, strength and resistance to thickness swell.
With certain products, protective overlays are applied during or after pressing. For example, a water-resistive overlay is integrated during pressing to create LP WeatherLogic® Air & Water Barrier. LP SmartSide siding gets an overlay during the pressing phase as well. For LP® TechShield® Radiant Barrier, a durable aluminum overlay is adhered after pressing.
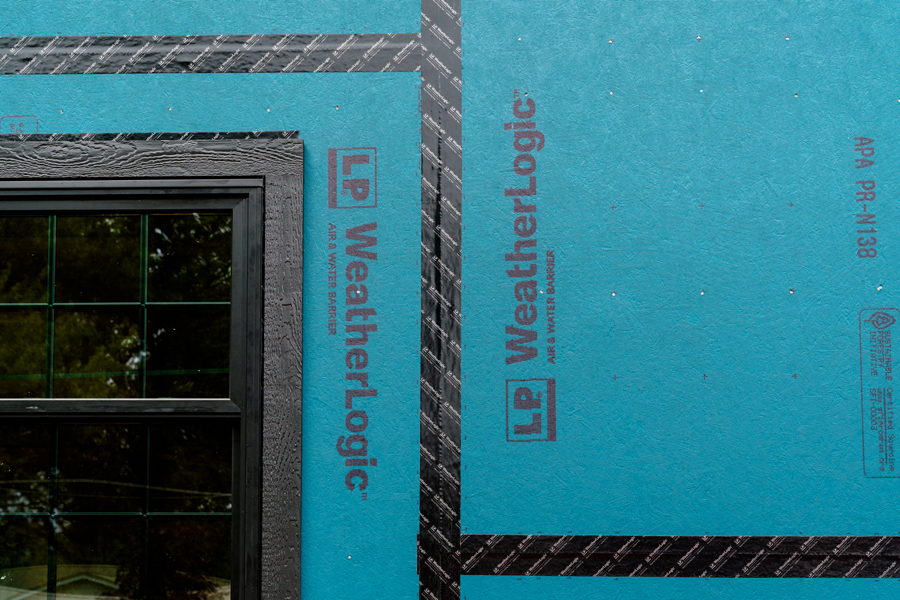
From there, the material is cut to size and sent for delivery.
Though the specifics of manufacturing vary from product to product, LP's unique processes set their products apart from other commodity OSB products, as well as other siding materials, so you can rely on advanced technology that helps you build better—and help you Build a Better World™.
Looking for more information about LP's collection of engineered wood products? Read more here.
Continue Reading
Resiliency Solutions
5 minIntroducing LP® SmartSide® ExpertFinish® Naturals Collection™: Nature-Inspired Beauty Meets Engineered Performance
We're excited to introduce the LP® SmartSide® ExpertFinish® Naturals Collection™, a bold new addition to our trusted line of engineered wood siding and trim that delivers the warmth and beauty of nature with the advanced protection and performance builders and homeowners expect.
Labor Solutions
5 minChoosing the Right LP® Structural Solutions Product for Your Build
When it comes to building strong, reliable, and high-performing structures, the materials you choose matter. At LP Building Solutions, we understand that every project, whether it's a single-family home or a multifamily development, requires structural components that meet your needs for strength, durability, and efficiency.
Sustainability Solutions
5 minBuilding a More Sustainable Future with LP Building Solutions
In today's world, sustainability is no longer just a buzzword, it's a blueprint for responsible living and smarter building. As the construction industry seeks ways to reduce its environmental footprint, LP Building Solutions is focused on providing innovative building materials for eco-conscious builders to help reshape what it means to build sustainably
News & Stories3 min
History of Partnership with Gary Sinise Foundation
The LP Foundation is a proud partner of the Gary Sinise Foundation, which supports wounded veterans in several ways. You can learn more about the LP Foundation here.